Powder Coating
Our Powder Coating Process
Powder coating is a dry finishing process used to apply a protective and decorative coating to various metal surfaces. It involves the application of finely ground particles, typically a combination of resin, pigment, and additives, onto a prepared substrate.
- Surface Preparation: The metal surface is cleaned to remove dirt, grease, rust, and other contaminants. This ensures proper adhesion of the powder coating.
- Powder Application: The powdered coating material is applied to the prepared surface using an electrostatic spray gun. The gun imparts an electrostatic charge to the powder particles, causing them to adhere to the grounded metal surface.
- Curing: Once the powder is applied, the coated metal is heated in a curing oven. The heat causes the powder particles to melt and flow together, forming a continuous film. The curing process also activates the chemical cross-linking reactions within the powder, resulting in a durable and hardened coating.
- Cooling and Final Inspection: After curing, the coated metal is allowed to cool down to room temperature. A final inspection is conducted to ensure the coating is uniform, smooth, and free of defects.
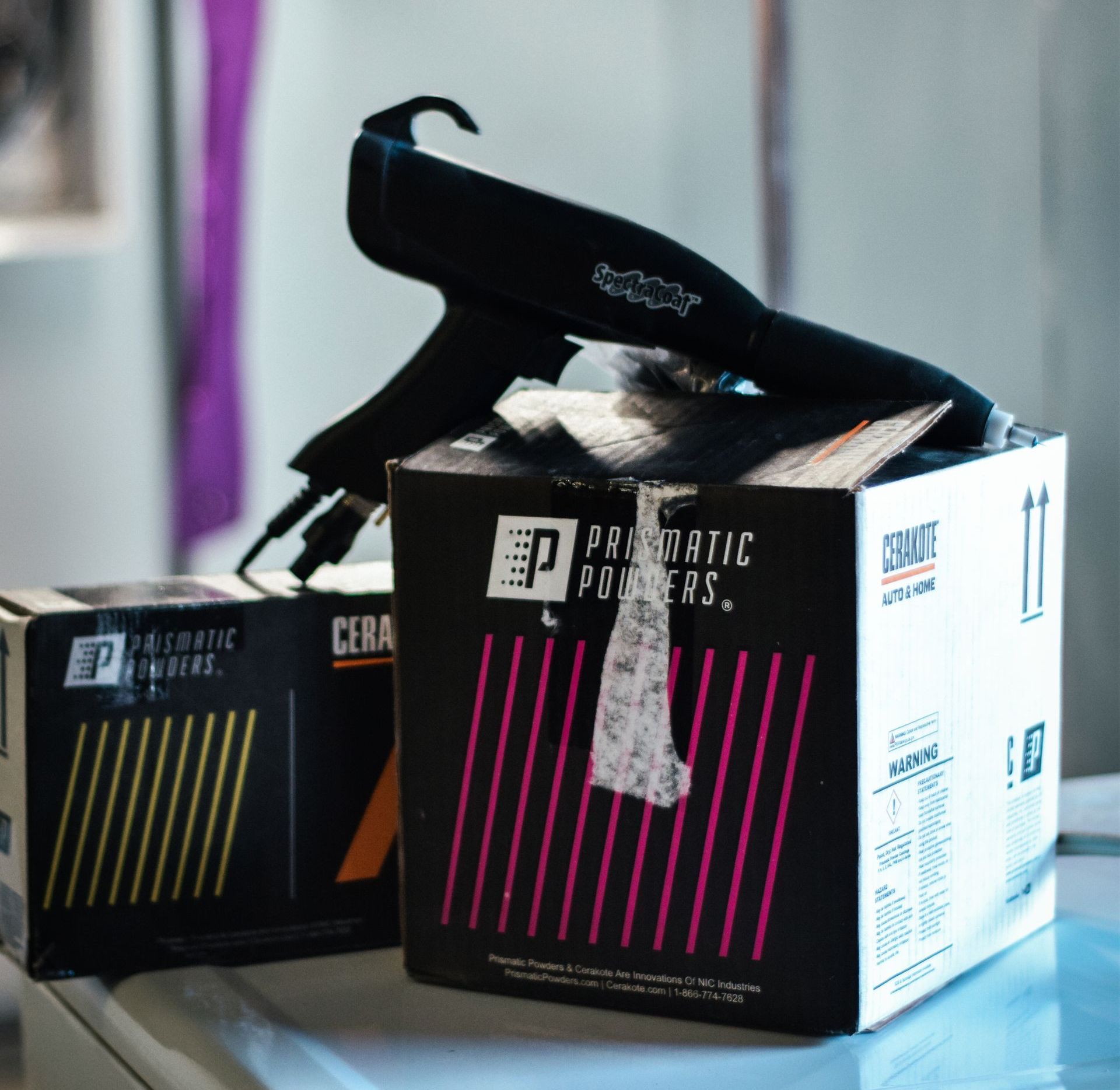
Powder coating offers several advantages over traditional liquid coatings
- Durability: Powder coatings are highly resistant to chipping, scratching, fading, and corrosion. They provide a tough and long-lasting finish, even in harsh environmental conditions.
- Wide Range of Colors and Finishes: Powder coatings are available in a vast array of colors, textures, and finishes, including glossy, matte, metallic, and textured. This versatility allows for customization and the ability to achieve various aesthetic effects.
- Environmentally Friendly: Powder coatings are solvent-free and emit negligible amounts of volatile organic compounds (VOCs), making them environmentally friendly. Excess powder can be reclaimed and reused, minimizing waste.
- Efficient Application: The electrostatic charge in the powder coating process ensures high transfer efficiency, meaning most of the powder adheres to the surface, reducing waste and overspray. This efficiency also allows for thicker coatings to be applied, providing enhanced protection.
- Faster Curing Time: Compared to liquid coatings, powder coatings typically have shorter curing times. This can lead to improved productivity and reduced production lead times.
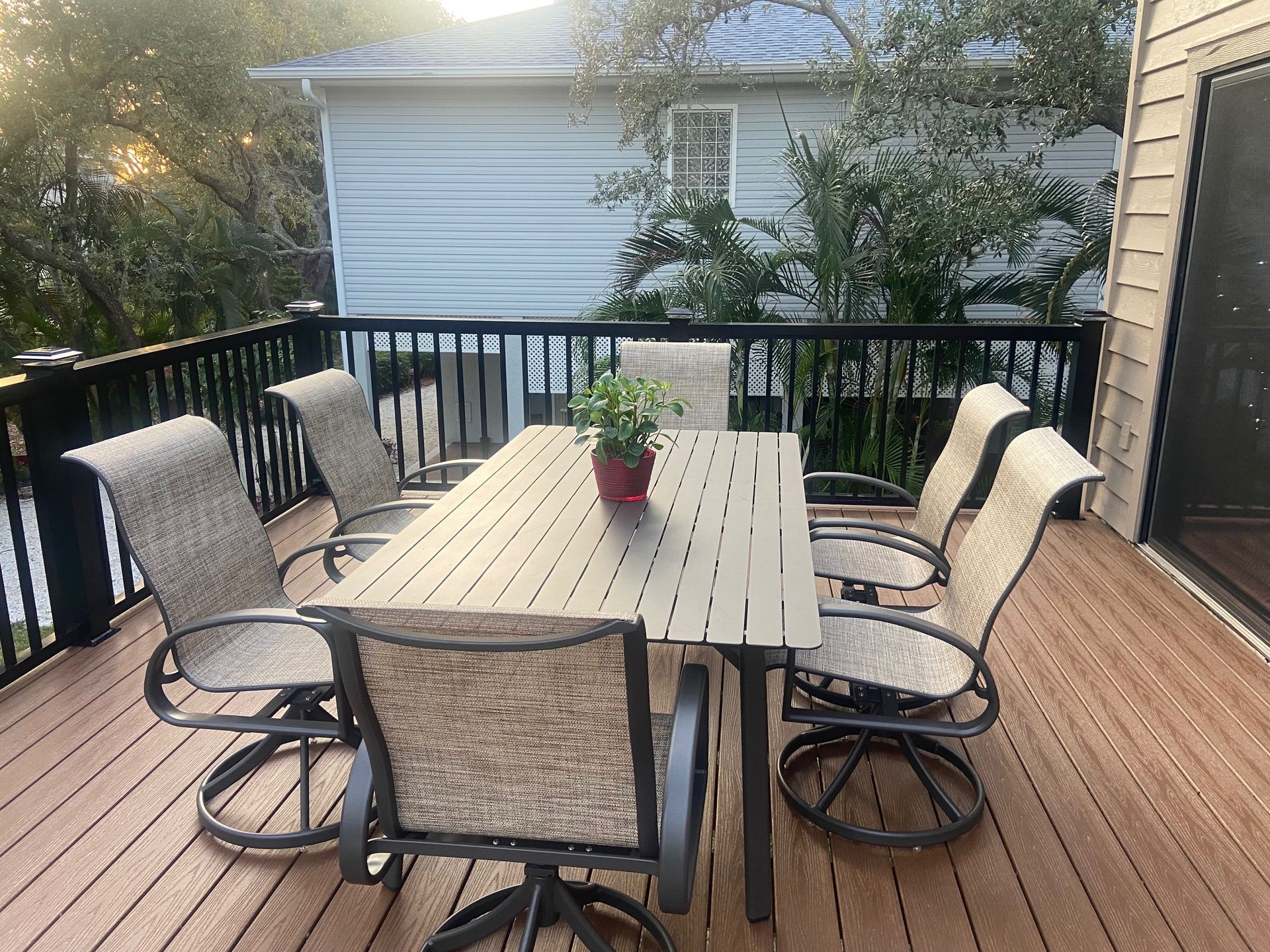
Powder coating can be applied to a wide range of metal surfaces:
- Steel: This includes carbon steel, stainless steel, and galvanized steel. Steel is one of the most commonly powder-coated metals due to its durability and wide range of applications.
- Aluminum: Powder coating is frequently used on aluminum surfaces, providing protection against corrosion and enhancing its appearance. Aluminum is commonly found in automotive parts, architectural elements, and outdoor furniture.
- Cast Iron: Cast iron surfaces can be powder coated to improve their aesthetics and resistance to rust and corrosion. Cast iron components such as engine blocks, machinery parts, and decorative items can benefit from powder coating.
- Brass and Copper: While less common than other metals, brass and copper can also be powder coated to provide a protective and decorative finish. This is often done for architectural applications, lighting fixtures, and decorative accents.
- Automotive Components: Many automotive parts are powder coated, including wheels, frames, chassis, bumpers, and engine components. Powder coating offers excellent durability and resistance to the elements, making it suitable for the automotive industry.
- Appliances: Household appliances such as refrigerators, ovens, dishwashers, and washing machines often undergo powder coating. This improves their appearance, durability, and resistance to scratches and stains.
- Furniture: Metal furniture pieces like chairs, tables, shelves, and outdoor furniture are commonly powder coated. It provides an attractive finish, protects against weathering, and enhances the longevity of the furniture.
- Architectural Elements: Powder coating is frequently used on architectural elements such as window frames, doors, railings, fences, and gates. It offers both protection and aesthetics, allowing for customization and color coordination with the overall design.
- Sports Equipment: Various sports equipment, including bicycles, golf clubs, fitness machines, and playground equipment, can be powder coated. It adds durability and an appealing finish while protecting the equipment from wear and tear.
We Partner With Prismatic Powders to Offer Over 300,000 Color Options
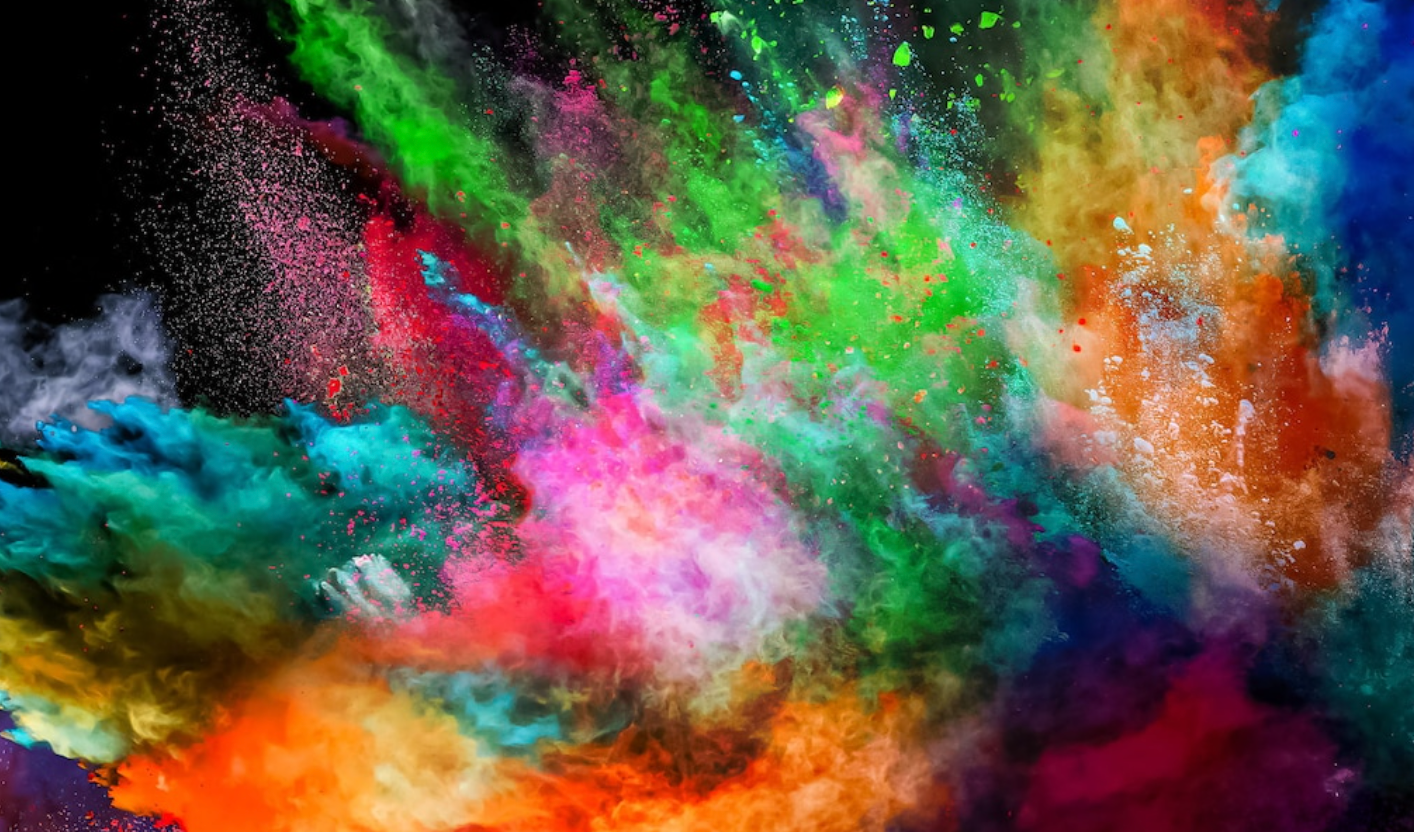